
一、生产代工与工厂布局
小米 SU7 由北京汽车集团越野车有限公司代工生产,工厂位于北京经济技术开发区,占地面积 71.8 万平方米,集研发、生产、测试、销售于一体。该工厂采用全自动化生产线,配备超过 700 台机器人,覆盖冲压、焊接、涂装、总装等核心工艺,每 76 秒即可完成一辆整车组装。工厂还布局了 16.2MW 分布式光伏电站,年均发电量约 1640 万度,年减少碳排放 9905 吨,相当于 54 万棵树的吸收量,实现了绿色能源的高效利用。
二、组装流程与技术亮点
- ** 高度自动化、组装流程与技术亮点
- 高度自动化生产
- 冲压与焊接:车身零部件通过 9 大工艺、60 多个设备控制 430 个参数,实现全自动化冲压与焊接,车身装配精度达 ±0.5mm。
- 涂装工艺:采用水性环保涂料(VOCs 含量仅 10%-20%)、锆化处理(替代传统磷化工艺,零重金属排放)及干式纸盒喷漆房,结合三室 RTO 直燃处理技术,VOCs治理效率超 99%,废水实现 “零重金属排放”。
- 总装与测试:电池包由宁德时代 / 比亚迪提供,电机来自苏州汇川,智能驾驶系统(Xiaomi Pilot)与座舱系统(HyperOS)通过自动化设备集成。整车下线后需经过 100% 紫外光外观检测、激光雷达在线检测等 6 大类工序,确保品质达标。
- 创新生产技术
- 一体压铸技术:应用于后地板等结构件,减少零部件数量,提升车身强度与生产效率。
- 模块化集成:在常州刹车盘工厂采用定制产线,碳陶刹车盘成本降低 60%,实现高端配置平民化。
- 生态链协同:小米生态链企业优先供应车规级芯片,采购周期缩短至行业平均的 1/3,保障供应链稳定性。
三、供应链体系与国产化水平
- 核心零部件供应商
- 电池:标准版随机搭载比亚迪刀片电池或宁德时代磷酸铁锂电池,高配版采用宁德时代三元锂电池。
- 电机:苏州汇川联合动力系统提供 TZ220XY102 型号电机,功率密度达行业领先水平。
- 智能系统:Xiaomi Pilot 智能驾驶系统自研,座舱搭载骁龙 8295 芯片,支持与小米生态设备无缝联动。
- 国产化率
小米 SU7 国产化率达82%-95%(不同统计口径差异),关键零部件如电池、电机、电控系统、芯片等均实现本土供应,符合国家产业政策导向。
四、交付进展与产能挑战
- 市场表现
截至 2025 年 4 月,小米 SU7 累计锁单超 43 万台,已交付约 21.6 万台,其中 2025 年 3 月单月交付量突破 2.9 万台,稳居新势力头部阵营。标准版等车周期长达 37-40周,积压订单超 15 万辆,反映出市场需求旺盛。
- 产能瓶颈与应对
北京工厂当前月均产能约 2.2 万台,年产能 30 万辆,难以满足需求。小米正加速推进北京二期工厂建设(2025 年年中投产,规划年产能 15 万辆),并规划武汉工厂,目标 2026 年实现 100 万辆产销量。
五、争议与挑战
- 电池混装策略
标准版随机混装比亚迪与宁德时代电池,虽分散供应链风险,但可能导致品控追溯困难。此前安徽 SU7 事故中,电池供应商信息未公开,凸显这一模式的争议性。
- 技术自主性
尽管小米强调自研电机与智能系统,但其电池热管理、快充技术仍依赖供应商,研发投入与特斯拉、比亚迪相比存在差距。
六、总结
小米 SU7 的组装生产展现了其在智能制造、绿色生产及供应链整合上的实力,高度自动化的工厂与创新技术应用确保了高效与品质。然而,产能不足与电池混装策略仍是当前主要挑战。随着新工厂投产与技术迭代,小米有望在 2025 年实现 35 万辆交付目标,并逐步提升技术自主性,向 “技术型车企” 转型。
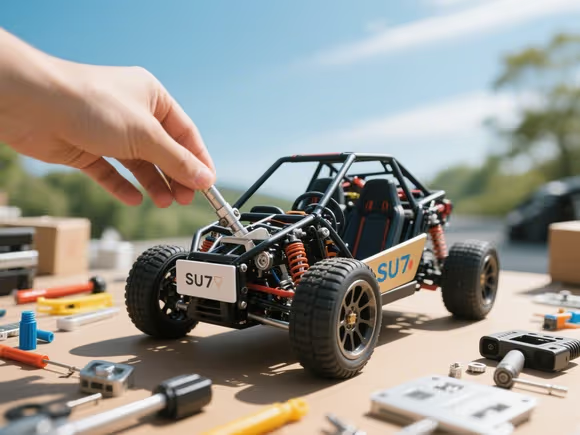