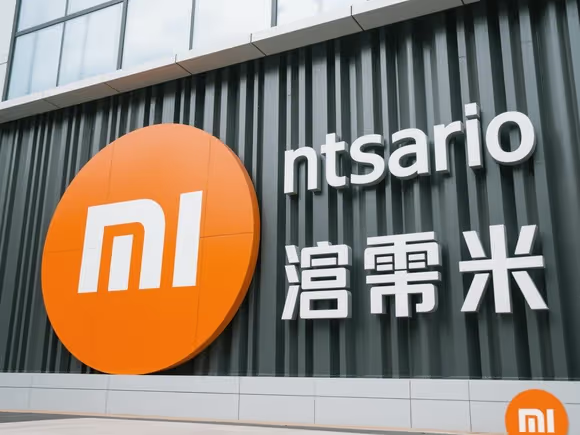
一、全球布局与核心工厂
1. 国内工厂:覆盖全产业链
- 北京昌平智能工厂
作为小米首个自有大规模手机工厂,总投资 24 亿元,年产能 1000 万台旗舰手机,生产小米 14 系列、MIX Fold 4 等高端机型。工厂采用全自动化生产线,配备自研工业数智平台(Hyper IMP),实现 “数据驱动、柔性敏捷” 的智能制造,关键工艺自动化率达 96.8%,获 “国家级智能制造标杆企业” 认证。 - 北京亦庄汽车工厂
小米汽车核心生产基地,一期年产能 15 万辆,二期规划产能 35 万辆。工厂拥有六大车间(压铸、冲压、车身、涂装、电池、总装),部署超 700 台机器人,关键工艺 100% 自动化,每 76 秒下线一台小米 SU7。其压铸车间采用 9100 吨锁模力设备,实现后地板一次成型;涂装车间支持 40 分钟快速换色,漆面精度达 ±0.5mm。 - 其他重要工厂
- 深圳工厂:生产智能手机、笔记本电脑及 IoT 设备,依托珠三角产业链优势,年产能超千万台。
- 天津工厂:专注智能电视和显示器生产,拥有先进的检测设备,年产能数百万台。
- 武汉工厂:布局智能家电,2026 年投产后将终结大家电代工依赖,生产效率提升 30%。
2. 海外工厂:本地化生产与市场拓展
- 印度工厂:共 7 座,与富士康、伟创力合作,年产能超 5000 万台手机,覆盖印度市场 95% 的需求。其中诺伊达工厂生产 Redmi Watch Move 智能手表,成为小米在印度本土化的新里程碑。
- 印尼工厂:位于巴淡岛,生产智能手机及 IoT 设备,辐射东南亚市场。
二、技术创新与智能制造
1. 自动化与机器人技术
- 汽车工厂:车身车间综合自动化率 91%,配备 400 余台发那科、库卡机器人,实现点焊、涂胶等工艺的 “黑灯生产”;总装车间采用机械臂自动化装配,精度控制在 ±0.5mm。
- 手机工厂:昌平工厂部署自研机器人,实现 SMT 贴片、板测、组装全流程自动化,日均产量 3 万台,人工干预率低于 1%。
2. AI 与数字化应用
- X-Eye 质检系统:基于 AI 大模型,检测准确率超 99.9%,效率比人工提升数十倍,用于小米汽车的电池包和车身检测。
- 数字孪生技术:在手机工厂中,通过虚拟模型实时优化工艺参数,例如根据 SPI 检测结果动态调整印刷机参数,提升良率。
3. 绿色制造
- 能源管理:北京汽车工厂屋顶光伏板年发电 1640 万度,相当于种植 54 万棵树;大压铸材料使用 30% 循环铝,涂装车间废气处理率 99%。
- 废水处理:汽车工厂采用预处理、中水处理等技术,实现 “零重金属排放”,循环用水比例达 50%。
三、供应链与可持续发展
1. 全球化供应链
- 供应商管理:与三星、索尼等全球供应商合作,通过严格的 ESG 审核和风险评估,确保原材料质量与可持续性。小米加入负责任商业联盟(RBA),推动供应链低碳转型。
- 本地化生产:在印度、印尼等地实现零部件本地化采购,降低物流成本,例如印度工厂 95% 的手机零部件来自本地供应商。
2. 可持续发展实践
- 循环经济:小米泰坦合金使用 30% 循环铝,包装材料采用 100% 可回收塑料,减少电子废弃物。
- 气候韧性:建立供应链自然灾害预警系统,通过大数据分析提前应对极端天气影响,保障生产连续性。
四、未来战略与挑战
1. 产能扩张
- 汽车领域:二期工厂 2025 年竣工后,总产能将达 50 万辆,目标 2025 年交付 35 万台小米汽车。
- 智能制造:未来十年计划新建 20 座世界级工厂,涵盖手机、汽车、家电等领域,进一步提升自研技术比例。
2. 技术突破
- 机器人研发:小米机器人公司已迁入亦庄汽车工厂,推进仿人机器人在制造场景的应用,计划 5 年投资 20 亿元。
- 芯片与系统:自研澎湃 OS 2 系统实现跨设备协同,V8s 超级电机刷新全球转速纪录,推动 “芯片 - 系统 - 终端” 全链路技术升级。
3. 挑战与应对
- 全球供应链风险:通过多元化布局(如墨西哥工厂规划)和本地化生产,降低地缘政治影响。
- 市场竞争:面对华为、特斯拉等对手,小米以 “性价比 + 生态协同” 为核心策略,例如小米汽车 SU7 通过 OTA 升级持续优化用户体验。
五、参观与开放
小米汽车工厂已开放常态化参观,游客可通过预约体验生产线观光、智能工厂餐厅及文创周边。北京昌平手机工厂也计划未来向公众开放,展示 “黑灯工厂” 的智能化魅力。
总结
小米工厂通过 “技术自研 + 生态协同” 构建了全球领先的智能制造体系,其布局不仅支撑了小米产品的高效交付,更推动了中国制造业的转型升级。未来,随着产能扩张和技术突破,小米有望在智能硬件和新能源汽车领域进一步巩固市场地位,同时以绿色制造和可持续发展为行业树立标杆。
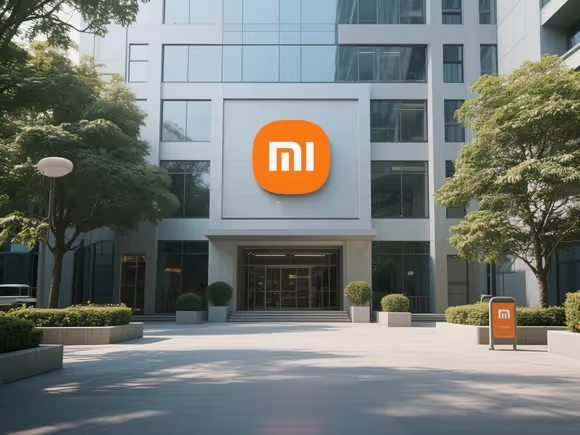